As part of our commitment to provide you with the most up-to-date and relevant information on the logistics industry, we share our Market Update on the Latin American market.
You will find information and interesting data on the update of the state of the ports, the most important transport routes and relevant news.
We hope you'll find the following information helpful, as well as inspiring to boost your business and keep your cargo moving.
Topic of the Month: Managing Supply Chain Disruptions: Strategies for Success
Managing supply chain disruptions has become a critical challenge for companies worldwide in today's fast-paced and ever-changing business environment. As we navigate through this year, in February, our focus will be on exploring effective strategies to mitigate these disruptions and ensure a resilient supply chain.
In today's interconnected world, supply chain disruptions can significantly impact businesses, leading to delays, increased costs, and strained relationships with customers and suppliers. However, with proactive planning and effective strategies, companies can mitigate these risks and maintain a resilient supply chain. By understanding and implementing these strategies, businesses can better prepare for unforeseen disruptions and maintain smooth operations.
Stay tuned as we share valuable insights and practical tips to help you manage supply chain disruptions and achieve success in your operations.
Supplier Diversification
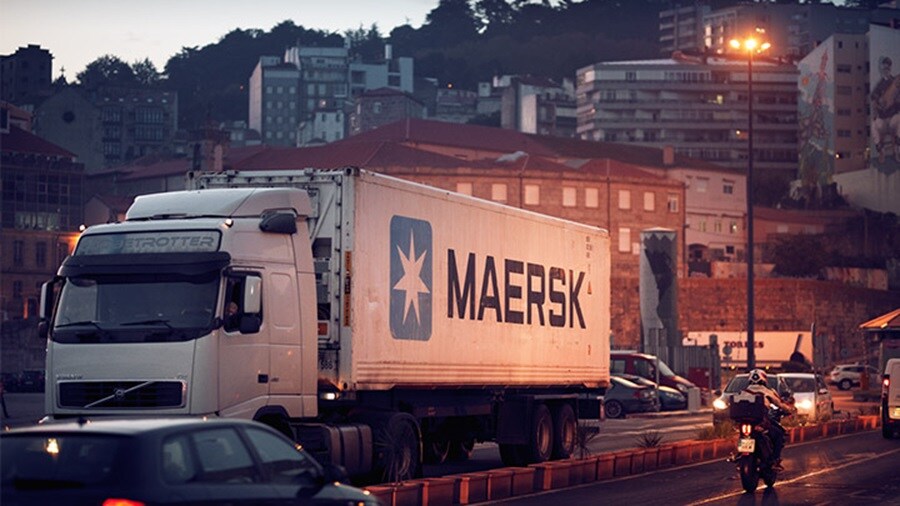
In the face of increasing uncertainties and potential disruptions, it is crucial for businesses to adopt strategies that enhance the resilience of their supply chains. Diversifying your supplier list is essential for filling in gaps whenever one of them suffers delays. While many companies tend to rely on a single supplier due to cost savings and practicality, expanding your supplier base will bring more resilience. According to a study by Deloitte, companies that diversified their suppliers experienced a 20% reduction in supply chain disruptions. There are several ways to achieve this, such as increasing the actual number of suppliers or spreading them geographically. By doing so, you can reduce the risk of disruptions and ensure a more stable supply chain.
For example, during the COVID-19 pandemic, companies that had diversified their suppliers were able to adapt more quickly to the disruptions caused by lockdowns and transportation delays. This strategy not only helps in mitigating risks but also fosters innovation and competitiveness by leveraging the strengths of different suppliers.
By implementing supplier diversification, businesses can create a robust supply chain that minimizes risks and enhances overall resilience. This approach ensures that operations continue smoothly even in the face of unexpected challenges.
Visibility
Enhancing supply chain visibility is crucial for identifying and addressing potential disruptions before they escalate. By implementing advanced technologies and robust communication systems, businesses can gain real-time insights into their supply chain operations and make informed decisions.
- Real-Time Tracking: Utilize technologies such as IoT devices, GPS trackers, and RFID tags to monitor the movement of goods in real-time. This provides visibility into the status of shipments, enabling quick responses to delays or disruptions.
- Data Analytics: Leverage data analytics to identify patterns and predict potential disruptions before they occur. By analyzing historical data, companies can understand trends and prepare for similar events in the future.
- Communication Systems: Establish effective communication channels that facilitate rapid information sharing between suppliers, partners, and customers. This ensures that all stakeholders are informed and can collaborate to address any issues that arise.
Build Strong Relationships with Suppliers
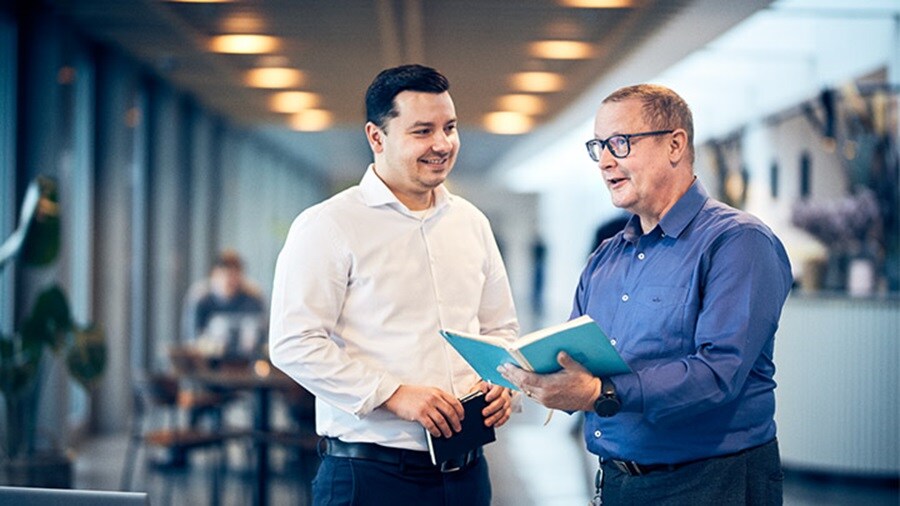
Maintaining strong relationships with your suppliers is crucial for effectively navigating disruptions. Open communication and collaboration can lead to better problem-solving and quicker recovery from any issues that arise.
Open Communication: Establish regular communication channels with your suppliers to ensure transparency and timely information sharing. This helps identify potential problems early and address them before they escalate. According to a study by Harvard Business Review, companies that maintain open communication with their suppliers can reduce supply chain disruptions by up to 30%.
Collaboration: Work closely with your suppliers to develop joint strategies for managing disruptions. Collaborative efforts can lead to innovative solutions and a more resilient supply chain. A report by the American Public University System highlights that effective collaboration with suppliers can lead to a 20% improvement in supply chain efficiency.
Trust and Reliability: Build trust with your suppliers by honoring commitments and maintaining reliability. A strong foundation of trust can lead to more flexible and supportive partnerships during challenging times. Research from the Journal of Operations Research indicates that companies with high levels of trust in their supplier relationships experience 25% fewer supply chain disruptions.

By fostering strong relationships with your suppliers, you can create a more resilient supply chain that is better equipped to handle disruptions and maintain smooth operations.
Develop Contingency Plans
Having contingency plans in place is crucial for responding quickly to disruptions and minimizing their impact on your supply chain. These plans should include alternative transportation routes, backup suppliers, and emergency response protocols.
- Alternative Transportation Routes: Identify and establish alternative transportation routes to ensure the continuous flow of goods. This proactive approach can help maintain supply chain operations during unexpected events.
- Backup Suppliers: Diversify your supplier base by identifying and partnering with backup suppliers. This ensures that you have alternative sources for critical materials and components. Research indicates that companies with backup suppliers experience significantly fewer supply chain disruptions.
- Emergency Response Protocols: Develop and implement emergency response protocols to address various types of disruptions, such as natural disasters, cyber-attacks, and geopolitical issues. Organizations with well-defined emergency response plans can reduce the impact of disruptions by a substantial margin.
By developing comprehensive contingency plans, businesses can enhance their resilience and ensure the continuity of their supply chain operations, even in the face of unexpected disruptions.
In an ever-evolving global landscape, managing supply chain disruptions requires a proactive approach that includes supplier diversification, enhanced visibility, strong partnerships, and well-defined contingency plans. By implementing these strategies, businesses can build resilience, minimize risks, and maintain operational stability.
At Maersk, we understand the importance of supply chain resilience and work closely with businesses to navigate challenges and keep goods moving efficiently. With a focus on end-to-end logistics solutions, we continuously adapt to industry changes to help our customers stay ahead.
As disruptions remain an inevitable part of global trade, companies that prioritize strategic planning and collaboration will be better positioned for long-term success. Stay agile, stay informed, and take action today to strengthen your supply chain for the future.
Ocean updates
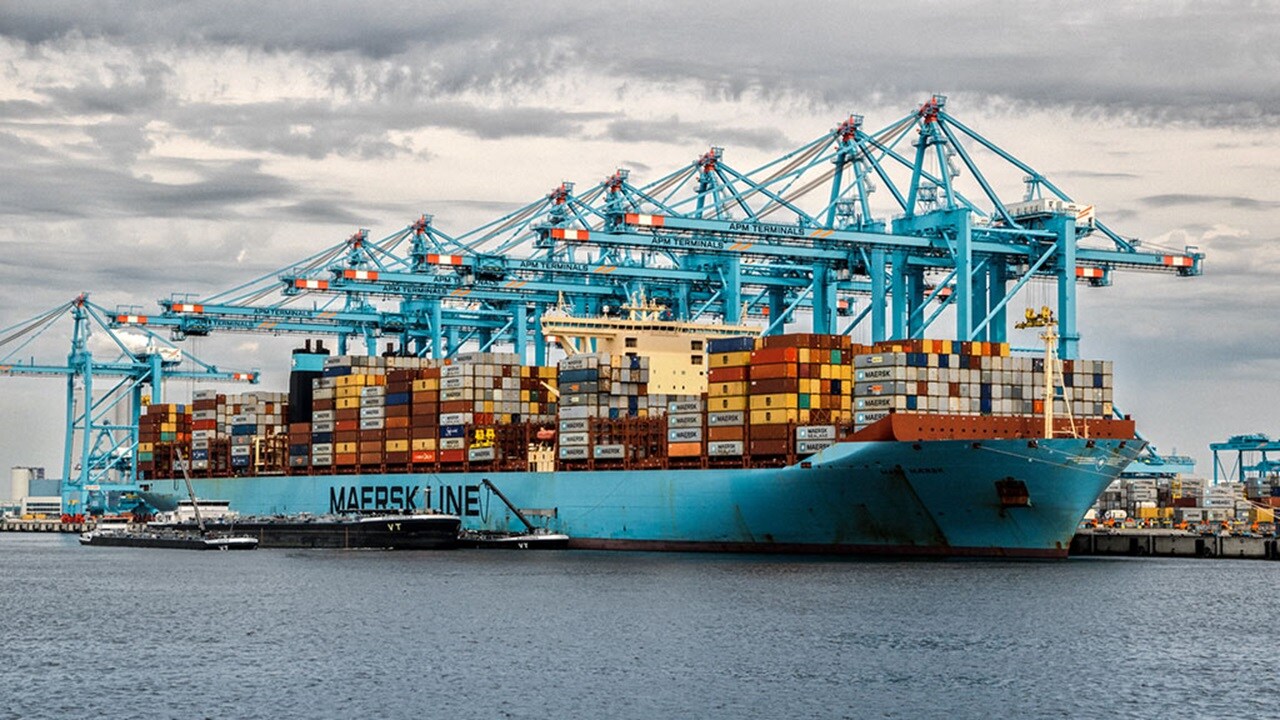
Trade lane | Comments |
---|---|
Trade lane
North America to Intra-Americas
|
Comments
The Bonita service will have its last call at Port Everglades, FL, on March 31, 2025, on the CC Fort St. Louis 514S. As an alternative, customers may continue to book from Port Everglades, FL, on our AGAS service, which has a fast transit time to our Panama hub for further connections to Kingston, Jamaica, and La Guaira & Puerto Cabello, Venezuela. Due to severe congestion and delays at the Savannah port, our North Atlantic Express (NAE) service will be temporarily omitting Savannah starting with the Polar Costa Rica 505S. We will closely monitor the situation and will provide updates once Savannah port calls can be resumed. South Atlantic Express (SAE) service will move from Virginia International Gateway (VIG) to to Norfolk International Terminal (NIT) in Norfolk starting November 16, 2024. First SAE vessel calling Norfolk International Terminal (NIT): |
Trade lane
West Coast to North America
|
Comments
Our Coquimbo coverage will be until week 8 with vessel Polar Peru 506N as the season moves to the Central Zone. We will continue focusing on the reefer from Chile to the U.S.
|
Trade lane
Intra-America to Caribbean
|
Comments
The Bonita service will have its last call in Colombia per the following: |
Trade lane
Central America to North America
|
Comments
The Bonita service will have its last call in Central America per the following: Due to severe congestion and delays at the Savannah port, our North Atlantic Express (NAE) service will be temporarily omitting Savannah starting with the Polar Costa Rica 505S. We will closely monitor the situation and will provide updates once Savannah port calls can be resumed. The South Atlantic Express (SAE) service will move from Virginia International Gateway (VIG) to Norfolk International Terminal (NIT) in Norfolk starting November 16, 2024. First SAE vessel calling Norfolk International Terminal (NIT): |
Trade lane
East Coast of South America to Intra-Americas
|
Comments
Peak Season Surcharge (PSS) for the Dry and Reefer cargo removed for all Intra-America destinations as of January 16th; |
Main port status
CARPAC Update: Callao/APMT is experiencing delays and congestion due to a port closure that occurred two weeks ago. We anticipate operations will return to normal by week 3. This terminal is also affected by a labor shortage, as many workers have been reassigned to other terminals. However, contingency plans are already in place to address these issues. Other terminals in this region are also facing challenges, with wait times exceeding one day. These delays are primarily due to port congestion, high yard density, and reduced productivity caused by a lack of resources.
ECSA Update: Terminal line up, Gate and yard running under healthy levels, although with some restrictions for vessels.
NAM Update: As our new Gemini Network approaches, we are diligently working with terminals and continuously working toward improved berthing lineups. However, we have been experiencing one of the roughest winter events in some of our ports (even snowfall, which wasn't predicted before). This is hampering wait times across our East Coast region, especially in ports like Newark, Norfolk, Savannah, Charleston, and Houston. On the Pacific side, we continue working with terminals and landside teams For Gemini.
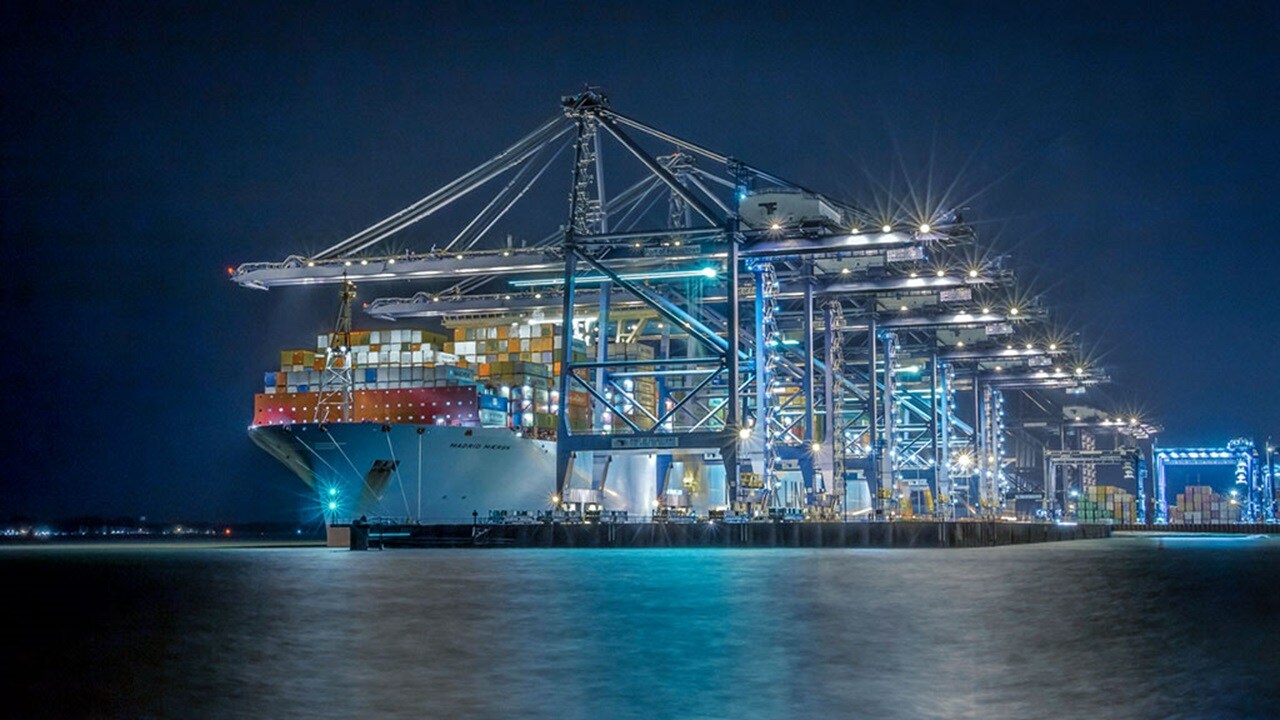
Port Status
1 - 3 Days | 4 - 7 days | More than 7 days | |
---|---|---|---|
Latin America
|
1 - 3 Days
Caucedo, Puerto Barrios, Sto Tomas de Castilla, Puerto Cortes, Lazaro Cardenas,Mx, Callao/APMT
|
4 - 7 days
Corinto
|
More than 7 days
Acajutla
|
Rest of World
|
1 - 3 Days
Norfolk, Charleston, Oakland
|
4 - 7 days
Savannah, Houston, Vancouver
|
More than 7 days
|
(*) - cargo connections can be impacted considering the delays reported
Landside updates
Central America, Andina and the Caribbean Sea Area
Regulatory changes for 2025 - SICETAC Colombia
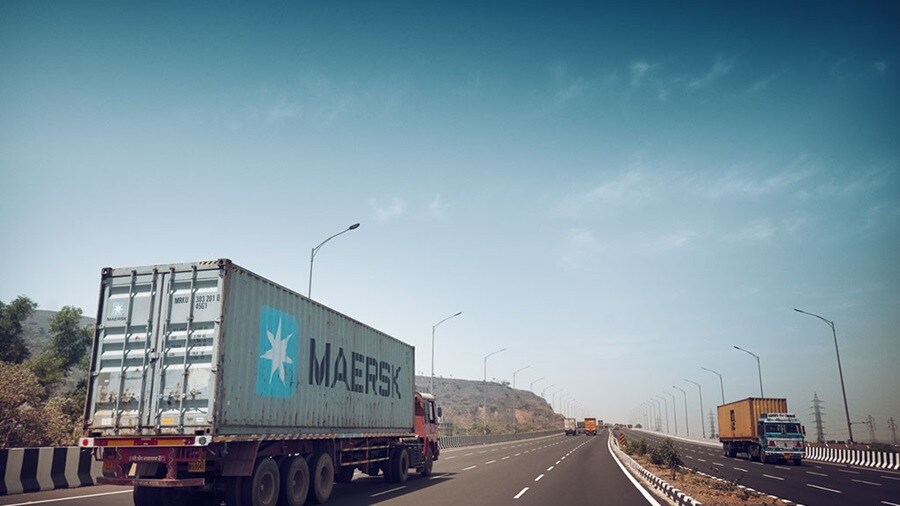
On February 1st, the Ministry of Transport of Colombia implemented a new adjustment in the Colombian market under modifications to the Integrated Control and Evaluation System for Freight Motor Transport (SICETAC). The adjustment established a minimum of 8 hours per trip as the basis for the minimum transport price, distributed among waiting time, loading, and unloading.
Among the provisions of this regulation are adjustments in minimum tariffs by distance, where routes less than 50 km will see an average increase of 51%, routes between 51 and 100 km an increase of 30%, and routes between 101 and 150 km an increase of 20%. One of the most significant changes in the new regulation is the mandatory real-time monitoring of the turn time, which will be introduced as of November 30, 2025 of loading and unloading via GPS.
All transport services must comply with the new regulation, ensuring adherence to this and its subsequent updates.
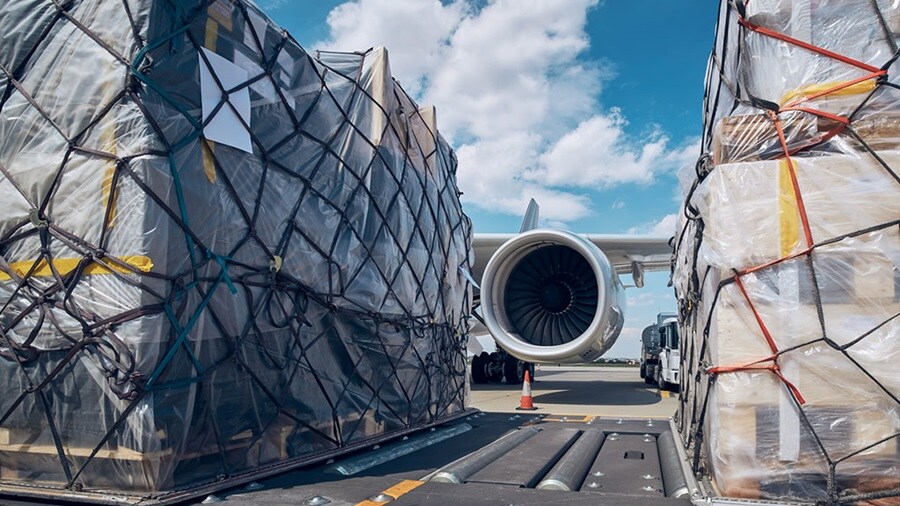
Air updates
Central America, Andina and the Caribbean Sea Area
Capacity to the CAC area is stable, and imports from Asia, Europe, and the Americas are performing as usual without any constraint. Regarding exports, the only trade to monitor closely is Colombia due to San Valentine's seasonality, expected to last until February 14th.
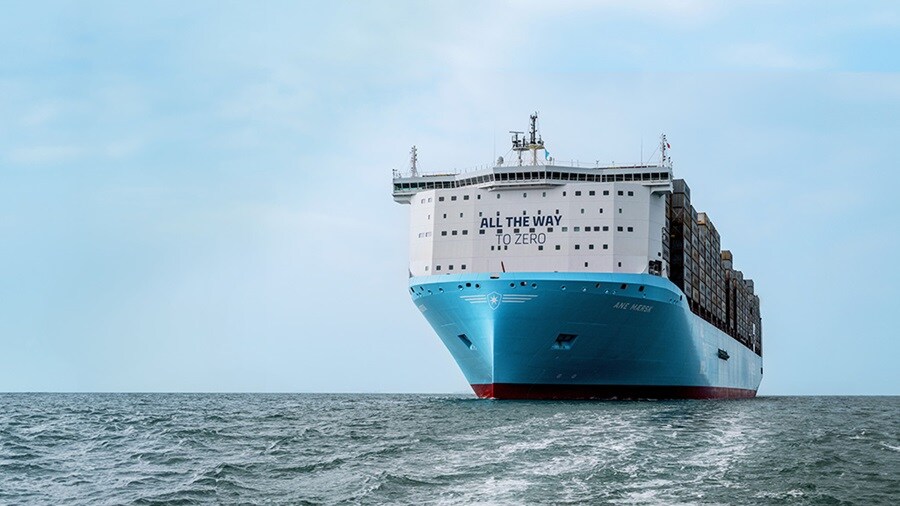
Highlights
Maersk reports third-best financial year
Copenhagen, Denmark – A.P. Moller - Maersk reports strong financial results for 2024 with growth across all segments and significantly improved profitability with EBIT increasing 65% to USD 6.5 billion. Results were driven by higher container demand and elevated freight rates in Ocean, top line and volume growth in Terminals and solid improvements in most Logistics & Services products. Given the strong results and the strength of the balance sheet, the Board of Directors proposes a dividend of DKK 1,120/share and also separately announced the initiation of a share buy-back programme of up to around USD 2bn to be executed over a period of 12 months.
Learn more from the global Maersk team
Learn what’s happening in our regions by reading our Market Updates by region.
Europe
North America
Asia Pacific
Be sure to visit our “Insights” pages where we explore the latest trends in supply chain digitization, sustainability, growth, resilience, and integrated logistics.
Anything you need, we’re here to help
By submitting this form, I agree to receive logistics related news and marketing updates from A. P. Moller-Maersk and its affiliated companies via e-mail. I understand that I can opt out of such Maersk communications at any time. To see how we process your personal data, please see our Privacy Notification.