One of the key takeaways from the pandemic and its aftermath, is the importance of resilience in supply chains. Unforeseen challenges have resulted in delays and headaches in logistical networks, causing barriers in ensuring timely delivery of products to consumers.
Piloting in Bangladesh
Bangladesh is a production hub for many global companies and was an optimal place to pilot the Supply Chain Resilience Model (SCRM). The model, tailored to each individual company, is developed to help customers reduce supply chain risks and mitigate disruptive impacts through pre-planned procedures and structures, working before, during and after disruption.
It was piloted with Marks and Spencer (M&S), a globally leading grocery retailer and department store, renowned for their excellence in business continuity (2021 winner of Business Continuity Award & Most Effective Recovery Award, Business Continuity institute). Maersk and M&S have a longstanding partnership, with Maersk playing a pivotal role in their global supply chain. Coupled with M&S’ experience of producing products in Bangladesh, piloting together on the SCRM made sense.
Harnessing resilience
Acting as a woven interlocking series of safety nets, the SCRM identifies key areas, including supply chain mapping, critical processes, suppliers, routes, their logistical capabilities, and key dependencies, to identify, evaluate and mitigate risks and put alternative solutions, with clear continuity objectives, in place. Possible disruptive impacts to the supply chain (like site operation suspension, port congestion/close or IT outage) are met with the SCRM’s knowledge and tools, giving companies the right instruments to manage disruptions.
Events over the last 24 months (Covid-19, Brexit, Suez Canal) have again highlighted the criticality of organisations’ understanding & ensuring that they have Supply Chain Resilience. Maersk has played a key role in supporting Marks & Spencer with its strategic Supply Chain Resilience Assessment & Business Recovery Planning, including the SCRM. This partnership will continue and grow, so both organizations continue to enhance and improve their preparedness together through delivering Business as a Service and value proposition.
The SCRM in action
To better understand how to strengthen M&S’ supply chain resilience, a joint exercise was facilitated in the early stages of the SCRM pilot. Participants included supply chain leaders and resilience departments in both companies. Through the exercise, both parties streamlined crisis responses and contingency plans, exploring opportunities for more effective responses and preparation. This was then worked into the SCRM, strengthening it further.
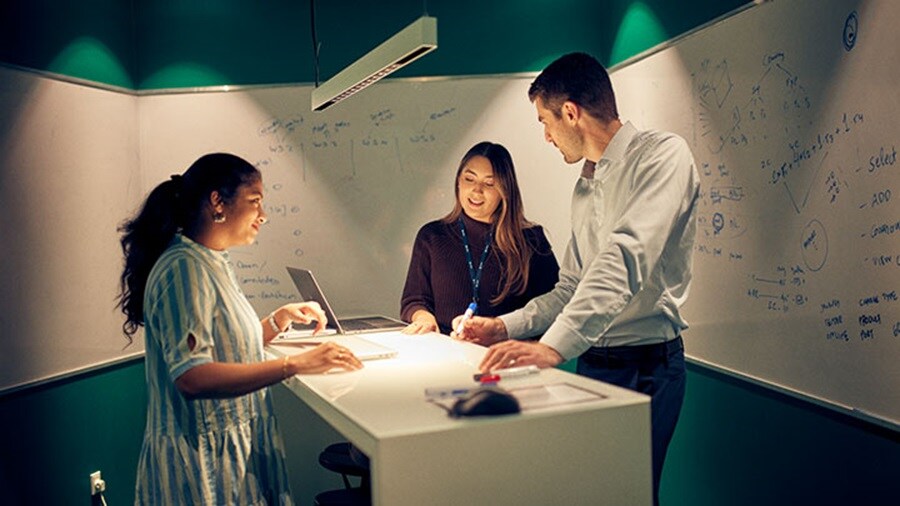
The SCRM’s pre-planned procedures successfully supported M&S through numerous challenges, including the trucking strike in Bangladesh and severe congestion at Dhaka airport.
A nation-wide strike of truckers took place in Bangladesh in September 2021, in response to raised income tax and the local road transport act. Working closely with shippers, carriers, warehouses, and stakeholders, Maersk ensured customers understood the developing situation. The team collaborated with carriers and warehouses, finding cut-off date extensions where possible and worked with port authority for late gate-in to minimise delays on delivery time.
Congestion at Dhaka airport, caused by a malfunction of scanning machines, resulted in extensive aircraft queueing with hundreds of tons of shipment delayed for over 20 days. To mitigate further delays and avoid the cost of truck waiting time, Maersk activated a SCRM-found alternative solution, utilizing sea-air mode to ensure delivery within acceptable lead times.
Each country brings its own set of challenges and along with it, own set of resilience skills. We have used this quality, our deep knowledge of the eco system in Bangladesh and detailed in sight of our customers’ business while partnering with M&S to develop the resilience plans for M&S. We sincerely hope that this will assist the customer and assure them of preparedness for alternate solutions to reduce the risks to their supply chain.
Weaving 'safety nets', creating opportunities
The SCRM further strengthens our customer’s ability to prepare for and handle disruptive situations, through effective risk management, pre-planned contingency solutions, and a capable customer service team with knowledge of disruption handling.
Maersk plans to continue to implement the SCRM across multiple verticals and expand the scope to cover major origin/destination countries and regions. Acting as a safety net woven of the many logistical areas we are experts in, the SCRM is an assurance of landside service reliability and resilience. With us, you can safely put all your eggs in one Maersk basket.
As your integrated logistics partner, we are here to support your business and future growth ambitions, so if you have not already, please feel free to reach out to our local teams to learn more about the SCRM and how it can be used in your supply chain.
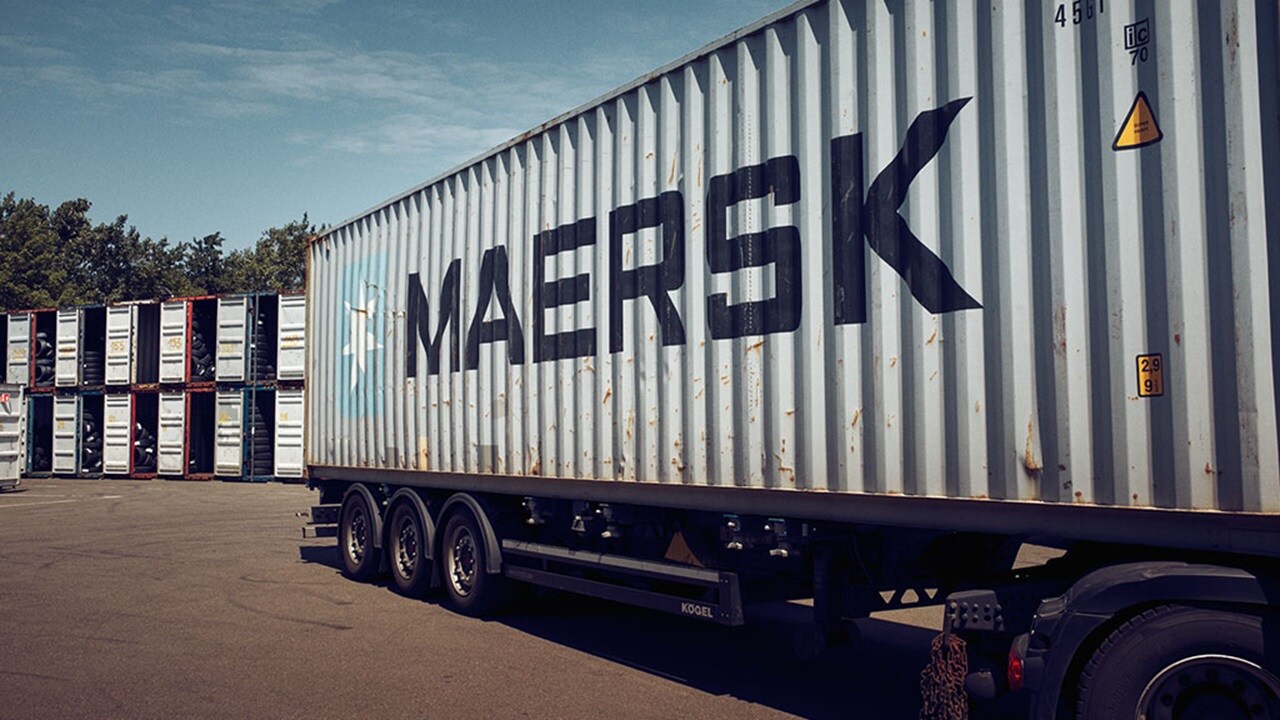
Anything you need, we’re here to help
By submitting this form, I agree to receive logistics related news and marketing updates from A. P. Moller-Maersk and its affiliated companies via e-mail. I understand that I can opt out of such Maersk communications at any time. To see how we process your personal data, please see our Privacy Notification.